Sensing & Vision Products from Robotiq
Robotiq designs and manufactures a variety of complementary components for use with collaborative robots.
Deploying sensors, cameras, finishing tools, and intuitive software with your robot makes automating your applications fast and easy. User friendly components and software ensure that operators of any experience level can quickly program and run the cobots; getting production going faster.
.jpg)
Force Torque Sensor
-
IP65 Rating
-
Stiff metal composition ensures high accuracy
-
Wear-free sensing technology doesn’t require calibration; no production downtime
-
Precise, repeatable, and high-resolution measurements
-
Constant force and stiffness for each axis
-
Precise object placement
-
Adjustable tool weight based on center of gravity
-
Includes Force Copilot intuitive programming interface
Specifications
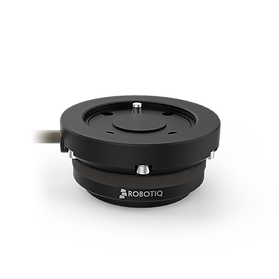

Wrist Camera
-
Easy vision hardware and software made for Universal Robots; operate with any expertise level
-
Locate different parts in a structured or unstructured environment
-
Adapts quickly to workplane and task changeovers
-
Create a visual model based on the CAD file of any part
-
Barcode and 2D reading
-
Automatic and manual adjustment of lighting, focus, exposition, and more
-
Teach, edit, and run via the Universal Robot teach pendant

Specifications

*All specifications provided for reference only. See user manual for official specifications.
Force Copilot
-
Force control made easy
-
Intuitive software to operate the Force Torque Sensor
-
Program complex robot movements in minutes; no robotics expertise needed
-
Increase robot cell reliability and flexibility
-
Uses the Force Torque Sensor data along with Force Copilot features to allow the programming of force-sensitive applications

Finishing Copilot
-
Software made for Finishing applications using cobots from Universal Robots
-
Save hours of programming
-
Generate a finishing path in minutes with fewer than 10 waypoints
-
Compensate for external tool wear
-
Set an external tool center point
-
Validates part position and automatically adapts all related parameters
-
Apply constant force and define the stiffness for each axis
-
Achieve .2 mm precision
-
Reset sensor values to zero
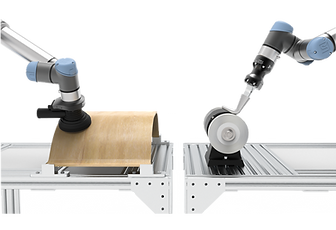
Our team of robotic specialists will work with you to find the best solution for your application, performing evaluations through proof-of-concept testing & time studies. We’ll help you select the ideal applications and then conduct simulations to test and demonstrate that the robot will meet your requirements.